1、Bottle conveying and sterilization: Empty bottles are conveyed via aseptic air conveyor with HEPA filters to ensure sanitation, and multiple bottle sterilizing / rinsing system keeps bottles extremely clean. No contact between filling valve and bottles.
2、Cap sterilization and conveying: After disinfectant soaking, and then dried by sterile water & air, eventually caps are conveyed to screwer via aseptic channel to keep extremely clean.
3、Beverage sterilization and conveying: Beverage treated by UHT sterilization and received by aseptic tank, then filled in filler block. To ensure the aseptic condition by means of internal & external mirror polished piping, aseptic pipe tie-ins, sanitary / aseptic valves & meters, and no dead angle.
4、Filling environment isolation, purification & preservation: Full-closed isolators on filling system with water seal. FFU and exhaust fan installed at proper air exhaust place. Rinsing area and filling area are isolated by partition board to ensure filling area achieving 100-grade air purification. Environment spouting alternately by spraying balls and nozzles. Roof-type sanitary filler platform to ensure aseptic filling environment.
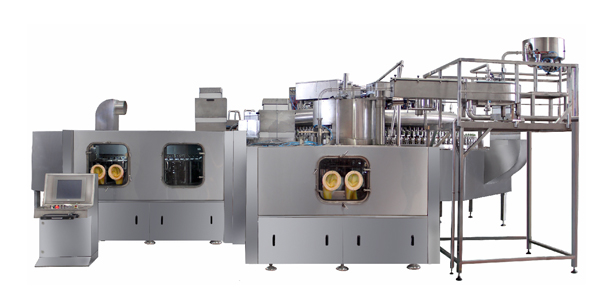